
But we did not reverse engineer this in the model which is why we see the yellow and red colors.Īs you can see, deviation bars and color maps are very handy for reverse engineering. The deviation here was the logo on the original part.

Prismatic shapes usually get a good fit depending on how worn a part is. And conversely, from light blue to dark blue is the reverse phenomenon – less material from scan to CAD model. Where you see colors going to yellow or red, that means the model has more material than the scan.
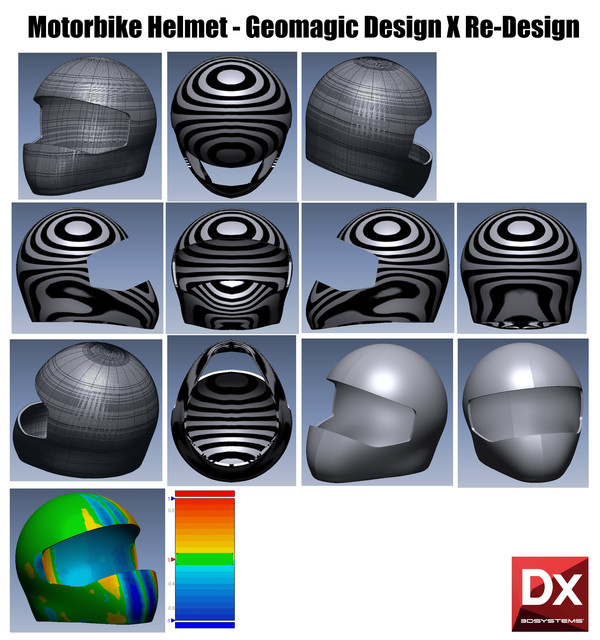
Similarly, if you loosen it to +- 9 thousandths of an inch, you will see the majority of the derived CAD model matches the 3D scan. If you tighten the tolerance to one-thousandth, you can see how the color map will change dramatically, with far fewer faces within tolerance. Resolution is the ability to pick up fine detail and scanners typically cannot see sharp edges, so in this case, you see tiny chamfer fillets on some of the edges. The reason you see the edges off is due to the scanner’s resolution. Everything you see in green is within +-4 thousandths of an inch of the scan. You can navigate to the Deviation for body tool. In this gas valve example below the derived solid model was created from a scanned mesh. But in most cases, you would typically want to correct the specifications to 2 inches. When reverse engineering, it is important to consider if you want to reverse engineer to your design intent, or simply reverse engineer as is.įor example, the scanned cylinders’ diameter may show up as 1.999827 inches. There could also be an error from the actual scanner.The second error could be that the part is worn or used.

